John Sealy Hospital Modernization
University of Texas Medical Branch at Galveston
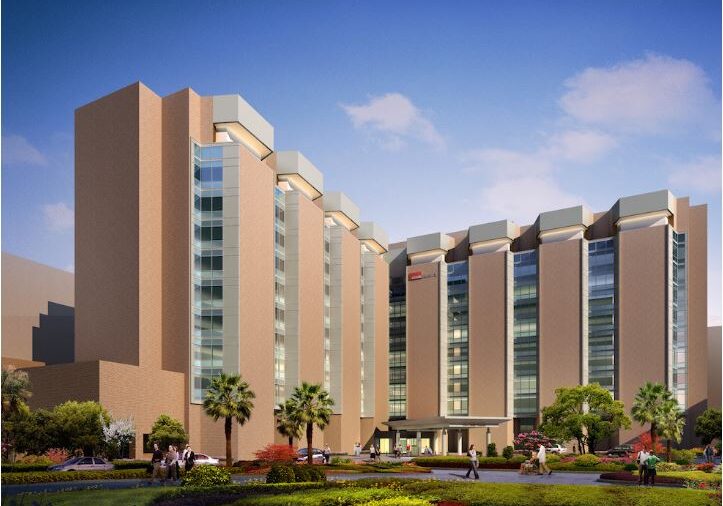
John Sealy Hospital was constructed in the 1970’s on the UTMB Campus. It consists of ten floors with two wings (AB and CD) with 256 patient rooms. This project will consolidate and expand the Women’s and Children’s services for the campus. SSA provided MEP Engineering for this project.
The project consists of two phases.
- Removal and replacement of the exterior skin.
- Renovation of levels 2-7 and partial renovation of levels 8-10.
The exterior skin replacement includes removing the entire brick façade and replacing with a new brick skin. In addition, the building floors will be enlarged to create larger patient rooms. The MEP portion of this project includes planning for revising the MEP services to the enlarged rooms. The actual design for the services into the spaces will occur in the interior renovation project. Also the skin replacement will install a new building entry canopy on the first floor.
The interior renovation project will be constructed concurrently with the reskin project. The interior renovation projects will encompass the following areas:
Level 2 – 27,564 GSF
Levels 3-7 – 137,753 GSF
Levels 8-10 – 82,700 GSF
This project will occur in phases, AB Wing and CD Wing. The CD Wing will remain occupied and functioning while the AB Wing is renovated.
The CD wing must be made ready to accept occupants from the AB wing. This includes minor renovations to allow a specific patient unit to function properly in an already existing patient unit. Part 2 of this renovation will be removal of the façade and buildout of the entire CD wing levels 2-10. The CD wing occupants will move into the newly renovated AB wing.
In addition to the renovation of the two wings there will be an MEP mitigation component to replace and relocate the building chilled water, heating water and domestic water system equipment from the ground level to level 2 out of the flood plain. New piping, valves and electrical panels have been provided for connection to mechanical equipment when mitigation projects is approved. This work has to be coordinated with a functioning building.
Mechanical Design
The owner had refurbished the original air handlers recently (replacement of coils, some rusting panels, etc.). SSA worked closely with the Owner and CMAR to conduct a cost/benefit analysis of replacing the refurbished air handlers with new units. A joint decision was made to provide new air handlers.
The existing systems do not meet the current energy or healthcare design standards. As a part of this project, new HVAC Systems for floors 2 through 12 was provided. Demolition of the HVAC system is phased such that one wing of the hospital is fully operational at all times. The core area between the two wings of this hospital will be phased to maintain access to the active wing.
New HVAC for the building is a VAV single duct system with hot water re-heat at each terminal. Outside air is provided to recirculating air handling units through 100% outside air pretreatment air handling units with energy recovery. Building general exhaust is drawn through the energy recovery units. Air handling units are located on the 11th floor and they are manifolded to provide redundancy. The HVAC system is sized to allow for one of the recirculating units to be offline for maintenance/filter changes without impacting the performance of the building.
Due to the existing structural floor to floor heights, there is an existing ductwork chase adjacent to each of the new patient rooms as well as 10 risers in the interior portions of the building. Ductwork risers throughout the building are being replaced as part of this project. Existing vertical chases are being repurposed from individual chases with hot and cold supply ducts with plenum returns in the chases. Chases will have a supply duct in one chase and ducted return in the other chase for each riser pair. This allows a fully ducted return to be installed throughout the building, complying with the latest codes and standards for inpatient hospital HVAC systems.
A dedicated HVAC system with redundant fans was provided for the new C-Section suite, due to the filtration and pressurization requirements.
Chilled and heating hot water risers are being replaced as part of this project. Pining design includes provisions to allow the future mitigation of the main chilled and heating hot water equipment to the second floor level to reduce the impact of flooding of the building HVAC systems. These provisions include additional valves and taps so that no hot-taps of piping are expected when the pump systems are mitigated as part of a future project.
Electrical Design
Demolition of lighting fixtures, receptacles, fire alarm devices and associated conduit and wiring was provided in areas being renovated. Existing panels, transformers and bus risers are being replaced. Electrical rooms are being expanded and stacked on each floor. Required outages for removal and installation of equipment was coordinated with the owner to maintain functionality for occupied spaces.
Building normal and emergency power is served from adjacent Building 6 switchgear, there is no distribution switchgear located in this building. Three new ATSs have been added as part of this project to provide adequate equipment branch power for mechanical equipment on 2nd Floor and 11th Floor.
New LED lighting fixtures are being provided per UTMB standards with occupancy sensors in office areas, to meet the energy code and switching in patient and staff areas. Multi-function fixtures are provided over patient beds with provisions for control by the patient bed nurse call device. Recessed, adjustable delivery room fixtures are provided in LDR rooms.
Receptacles on normal and emergency power are provided as necessary for required equipment and for patient headwalls. Plug load switching is provided per energy code.
A new fire alarm panel is being installed in the first interior renovation phase, new devices will be installed and connected to this panel. The existing fire alarm panel in the second level interior renovation phase is to remain active until that phase is under construction, then it will be removed. Fire alarm devices installed in the second interior renovation phase will connect to the new fire alarm panel.
Plumbing Design:
The plumbing scope consisted of replacement of all domestic, drainage waste/vent, and medical gas risers in the building, a complete gut-and-redo of levels 3-7 in the AB Wing, and a complete gut-and-redo of levels 4-6 in the CD Wing. This included new plumbing fixtures, new medical gas outlets and alarm panels, and the rough-in connections to new equipment.
The entire existing building was serviced by a single combination domestic and fire water supply which required creativity in design and construction to prevent or limit the downtime of the existing systems during construction. Also included in this project was the planning and design of a piping layout with connections for a future Level 1 mechanical equipment room flood mitigation project to allow the ease of relocating the plumbing, fire protection and mechanical pumps, heat exchangers and other miscellaneous equipment to Level 2 of the building.
Site Owner
University of Texas Medical Branch at Galveston
Location
Project Cost
$102,000,000
Project Completion
2021
Expertise
Services
Electrical Engineering
Mechanical Engineering
Plumbing Engineering