Central Plant and Infrastructure
Texas A&M University
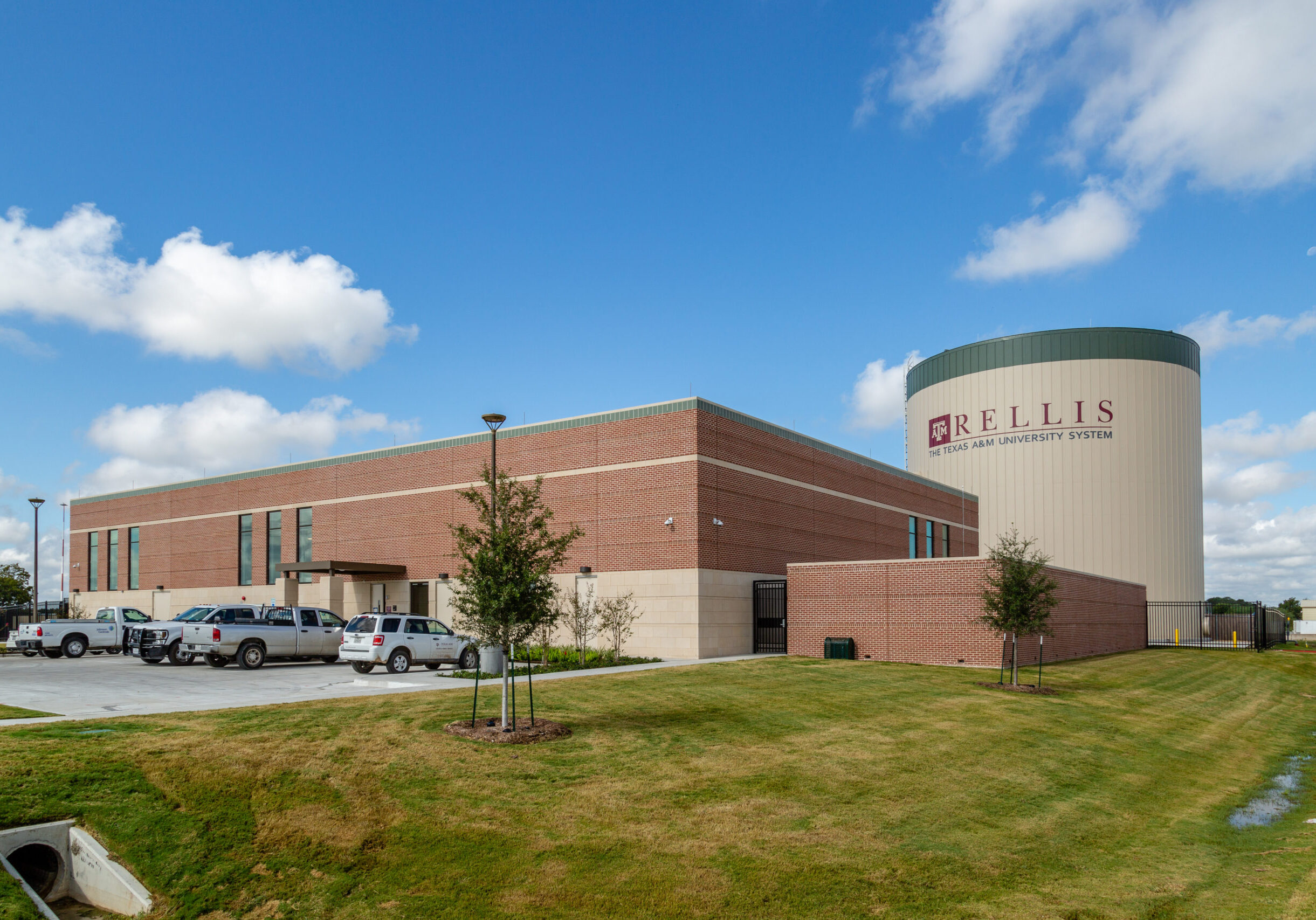
The Texas A&M University System RELLIS Campus is a premier, high-tech research, technology development, and education campus which is home to multi-industry education facilities and offers a variety of curricula. This project was for the central utility plant, and distribution piping as well as electrical distribution, infrastructure to support the first phase of the campus development including five buildings with a total of 580,000 SF.
The thermal utility plant was designed for superior energy efficient and fault tolerance to provide dependable services to the campus. To serve the cooling demand of 2400 tons and the heating demand of 12800 MBtuh with n+1 redundancy, the central thermal utility plant comprised of four 800 ton chillers, a 12,800-ton hr chilled water thermal storage tank, and six-3 MMBtuh boilers. The design of the centrally located thermal utility plant accommodates future expansion of the electrical, chilled water, and heating water systems as the campus grows.
The central plant also supplies electric power to the campus. The 12.47 kV electrical service from an underground ductbank connects to 2000 A, main-tie-main switchgear in the plant, and power is distributed to the 15 kV switches at the campus buildings via underground duct banks. Two-12.47kV-480V pad mount transformers serve loads at the central plant.
Chilled water was produced with VFD drive, magnetic bearing water cooled chillers in a variable primary. Variable secondary system including the thermal storage tank. SSA made an economic analysis to select the chiller equipment based on the best overall value. The control system included optimization of the chilled water production to configure the operation of the equipment including equipment selection, chilled water flow, condenser water flow, and condenser water temperature to minimize energy consumption.
Heating water was produced with modular dual fuel, condensing type boilers firing natural gas and configured for propane as a backup fuel.
The plant control system was designed for automatic operation with remote monitoring and utilizes redundant mirrored servers for dependable performance.
Site Owner
Location
Project Cost
$38,900,000
Project Completion
2017
Expertise
Central Plant
CUP & Infrastructure
Higher Education
Research
Services
Commissioning
Electrical Engineering
Mechanical Engineering
Plumbing Engineering